What is non conductive acrylic conformal coating for electronics?
What is non conductive acrylic conformal coating for electronics?
Conformal coating is an area everyone in electronic production, dealership, or maintenance and repair should be familiar with. The fact that electronic devices are used in all kinds of conditions makes it important to ensure they are well protected to keep them functioning right. Printed circuit boards are sensitive and can be termed as the brains of electronic devices. Their protection cannot be overlooked. Therefore, your device is as good as the circuit.
Conformal coatings offer protection to the boards and their components. They are thin resin films applied to keep elements such as moisture, dust, and high temperatures off the boards, so they function effectively and reliably.
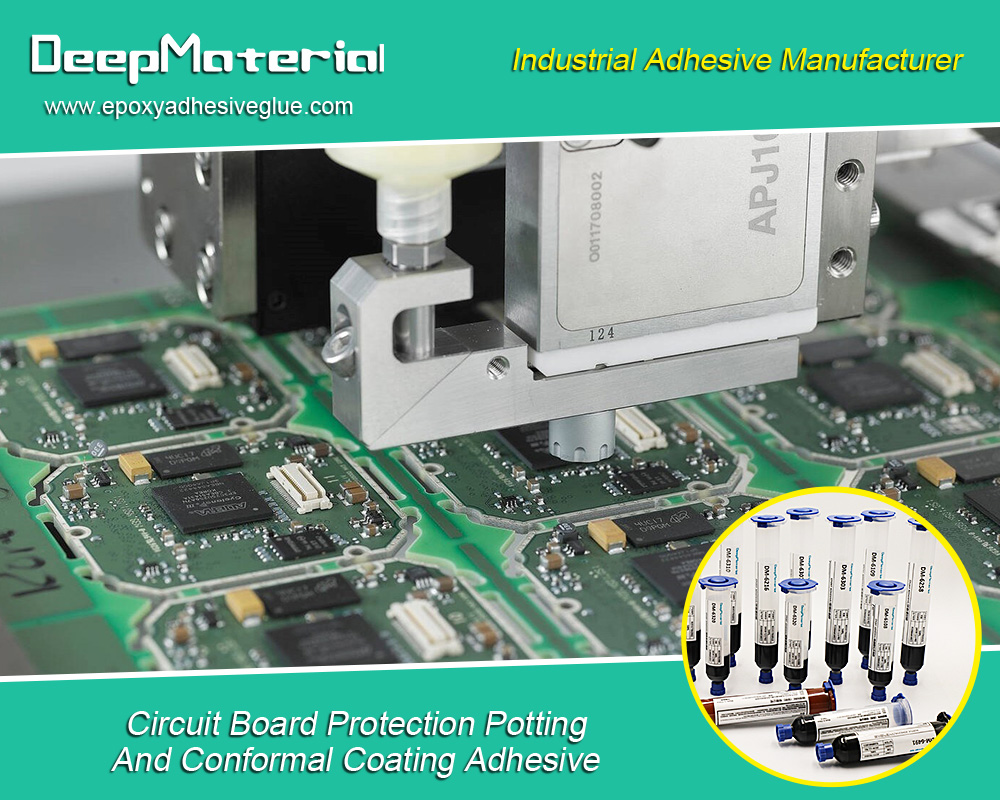
Acrylic resin, abbreviated AR, is among the most common conformal coatings. This single-component coating material offers an excellent barrier to humidity and moisture. The coating is also very good at keeping fungus away, making it one-of-a-kind. Pre-formed acrylic polymers are dissolved in solvents to prepare them for surface application. Acrylics conform to the electronic circuitry shape covering the entire surface and protecting it against physical and electrical elements that could be harmful. The coating can be used even on heat-sensitive devices because it produces minimal or no heat during the curing process.
Acrylic conformal coating is non-conductive and, therefore, withstands static discharge. These dielectric properties give PCB applications an advantage because product capabilities are enhanced through miniaturization. It simply means that the components can be closely designed. Hence, they are as small as possible, giving room for more components and capabilities in one assembly without interference with each other.
Acrylic coating properties
Acrylic conformal coating properties include:
- Clear coating
- Dielectric constant
- Quick drying
- UV traceable
- Low moisture absorption
- Ease of reworking
The application process
Like the other conformal coatings, the acrylic resin can be applied to the surfaces by way of:
Brushing – In this method, a small brush is used to produce the appropriate film. Hand brushing is particularly appropriate for small-scale batches and repair works. The operator must be careful to ensure the coating is done on the entire targeted area and each side of the device.
Spraying – This application method is best for large production quantities. It is considered the most accurate because the coating can easily be controlled. A spray gun would be all that’s needed for small volumes, whereas you can consider an automated robotic process for higher production volumes.
Dipping – The assembly is immersed in a tank filled with the acrylic conformal coating in this application method. You can do the dipping manually, or you can automate it with the right tools; it all depends on the needs and capabilities of the user.
The low chemical resistance of acrylic resin makes reworking easy. Components may require repairs and rework for one reason or another. With a common solvent, you can remove the existing coating and reworking on the device as required without any damage. Acrylics are also fast in curing. The coating will be dry to your touch within ten minutes, and within a day, it will be completely cured at room temperature. You can further decrease the curing by using thermal curing.
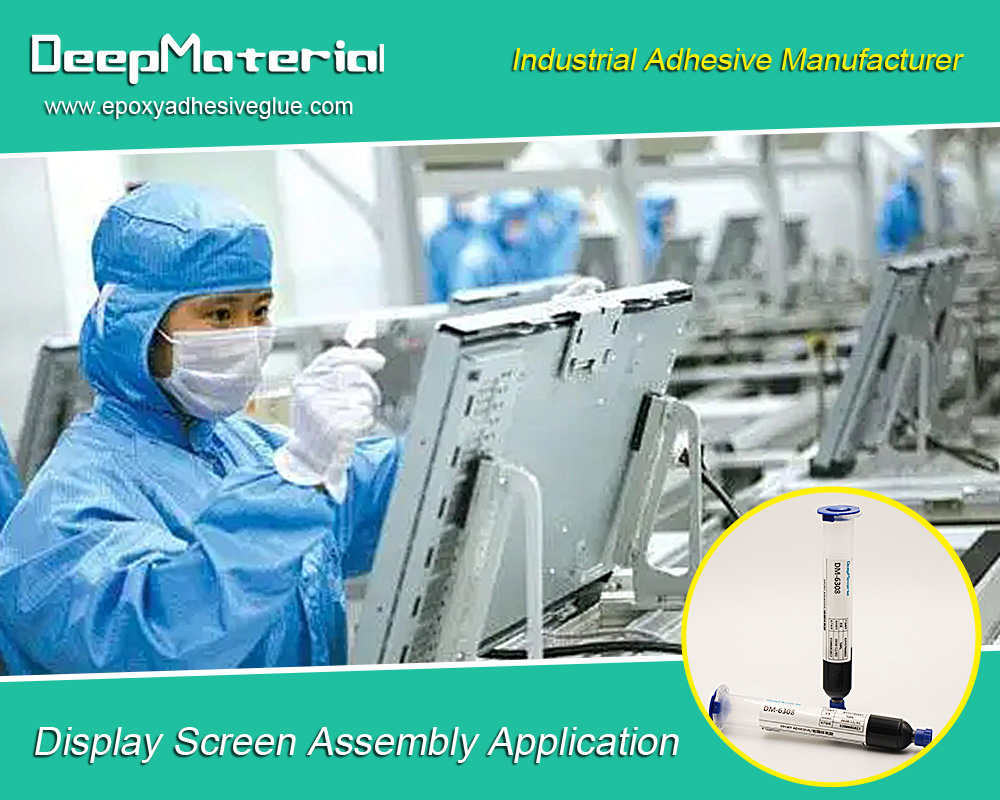
For more about what is non conductive acrylic conformal coating for electronics,you can pay a visit to DeepMaterial at https://www.epoxyadhesiveglue.com/what-is-acrylic-conformal-coating/ for more info.