What are the specific applications of electronic adhesives in the electronic manufacturing process?
What are the specific applications of electronic adhesives in the electronic manufacturing process?
Electronic adhesive, also known as conductive adhesive or electronic bonding material, is a special formulation of adhesive used in the electronics industry to connect or bond electronic components together. These adhesives are designed to provide both mechanical strength and conductivity, enabling them to establish reliable connections between various components. The application of adhesive in the electronic industry, in addition to mechanical fixation, also requires thermal conductivity, electrical conductivity, insulation, and adaptation to the impact resistance assembly, sealing, and protection substrate requirements. With the popularity of smartphones around the world, products with ultra-thin touch screens and intelligent systems are becoming popular among consumers. The development of smartphones is also constantly pursuing lighter, thinner, and more beautiful product designs. With the continuous development of electronic products, the requirements for adhesive materials and processes have also increased.
Electronic adhesives play a crucial role in the electronic manufacturing process by providing bonding and sealing solutions for various applications. Here are some specific applications of electronic adhesives:
Surface Mount Technology (SMT): SMT is a widely used method for assembling electronic components. Electronic adhesives are used to bond surface mount devices (SMDs) and adhere them to printed circuit boards (PCBs). Adhesives play a critical role in securing SMDs to the PCB before soldering. They provide reliable bonding and electrical connections, ensuring secure and durable component placement.
Component Bonding: Electronic adhesives are used to bond and secure various components onto printed circuit boards (PCBs). These components include resistors, capacitors, diodes, integrated circuits (ICs), connectors, and surface mount devices (SMDs). Adhesives ensure proper mechanical support and electrical conductivity between the components and the PCB.
Underfilling: Underfill adhesives are used to fill the gap between a chip and a substrate in flip-chip packaging. This helps in improving mechanical strength, reducing stress, and enhancing thermal conductivity, thus preventing damage due to thermal expansion and contraction.
Underfill adhesives typically have a low viscosity to facilitate their flow and penetration into the narrow gaps between the chip and the substrate.After curing, which can be achieved through various methods such as heat or UV light, the underfill adhesive solidifies, providing structural support and protection to the solder joints.
Underfill adhesives are commonly used in applications where the IC chips are subjected to significant thermal variations or mechanical stresses, such as in mobile devices, computer systems, automotive electronics, and other electronic devices with high-reliability requirements. They play a crucial role in improving the longevity and performance of these electronic products by enhancing the strength and reliability of the solder connections.
Potting and Encapsulation: Electronic adhesives are used for potting and encapsulating electronic components to protect them from moisture, dust, vibration, and other environmental factors. Encapsulation involves covering components with a protective layer of adhesive, while potting refers to completely embedding components in adhesive compounds. Potting compounds provide mechanical support and electrical insulation, ensuring long-term reliability and preventing damage from external elements.
Wire Bonding: Adhesives are used in wire bonding applications to attach fine wires (usually made of gold or aluminum) from the die to the substrate or leadframe. Wire bonding adhesives provide electrical conductivity, mechanical strength, and protection against wire movement or detachment, and ensuring reliable electrical connections. Wire bonding techniques include wedge bonding, ball bonding, and ribbon bonding.
Conformal Coating: Electronic adhesive conformal coatings are protective coatings applied to electronic components and PCBs. They serve as a barrier against environmental factors such as moisture, chemicals, dust, and temperature variations. The primary purpose of conformal coatings is to ensure the long-term reliability and functionality of electronic devices.It’s important to select the appropriate conformal coating material based on factors such as the specific application, operating environment, temperature range, chemical exposure, and desired properties. Different types of electronic adhesive conformal coatings include acrylics, silicones, urethanes, epoxy resins, and parylene, each with their own advantages and limitations.
Thermal Interface Materials (TIM): TIMs are adhesive materials with excellent thermal conductivity properties,and used to bond heat sinks, thermal pads, and other cooling devices to electronic components. They facilitate efficient heat dissipation and prevent overheating, ensuring optimal performance and reliability.
EMI/RFI Shielding: Adhesive-based conductive materials are used for electromagnetic interference (EMI) and radio-frequency interference (RFI) shielding in electronic devices. These adhesives provide a conductive path, blocking or diverting unwanted electromagnetic signals and preventing interference with sensitive components.
Display and Touch Panel Bonding: In the production of electronic displays and touch panels, adhesives are used to bond layers of glass, plastic, or other substrates together. Electronic adhesives used for display and touch panel bonding are typically optically clear, meaning they have high transparency to allow the display or touch panel to function properly. These adhesives are also formulated to have excellent adhesion to various substrates, such as glass, plastic, and metals, while maintaining good flexibility. Similar to Optical Clear Adhesives, Liquid Optical Clear Adhesives are also used for bonding touch panels and displays. Liquid Optical Clear Adhesives are in liquid form and applied as a thin layer between the layers of the display or touch panel. They cure when exposed to UV light, forming a transparent and durable bond.
Repair and Rework: Electronic adhesives are also used in repair and rework processes. They enable the removal and replacement of faulty components, as well as the reattachment of loose or damaged parts. Electronic adhesives are widely used in the manufacturing and repair of electronic devices. They provide bonding and sealing properties that are essential for component attachment, protection against moisture and contaminants, and electrical insulation. When it comes to repair and rework, electronic adhesives play a crucial role in ensuring the integrity and functionality of the repaired components or circuitry. When repairing or reworking electronic components, it is important to choose the right adhesive for the specific application. There are various types of electronic adhesives available, including epoxy, cyanoacrylate (super glue), UV-curable adhesives, conductive adhesives, and thermal adhesives. Consider the requirements of the repair, such as mechanical strength, thermal conductivity, electrical insulation, or conductivity, and select an adhesive that meets those needs.
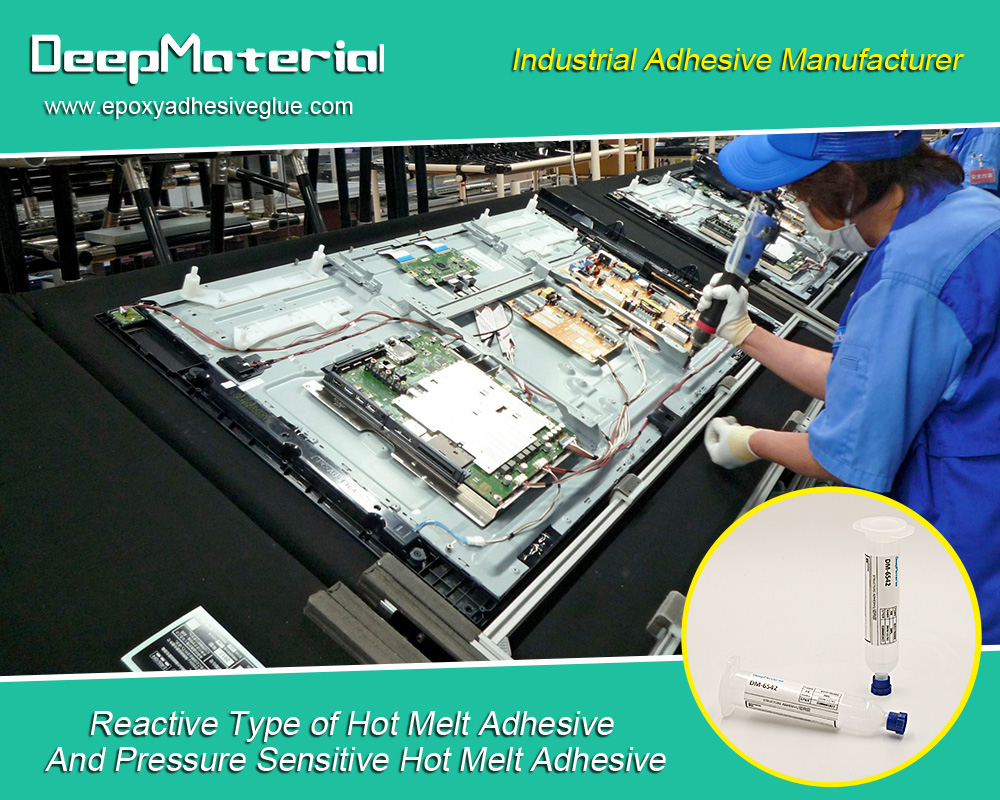
It’s important to note that these are just a few examples of the applications of electronic adhesives in the electronic manufacturing process. The specific type of adhesive used depends on the requirements of the application, such as electrical conductivity, thermal management, environmental protection, or mechanical strength. Each application can vary based on factors such as substrate materials and manufacturing processes, so when selecting the appropriate adhesive for a particular electronic assembly, the manufacturers often work closely with adhesive suppliers or rely on material engineers to choose the most suitable adhesive for their specific needs.
For more about choosing the best electronic adhesive,you can pay a visit to DeepMaterial at https://www.epoxyadhesiveglue.com/category/electronic-adhesives-glue/ for more info.