The Science behind Metal Bonding Epoxy Adhesives: Understanding The Chemical Reaction
Metal bonding epoxy adhesives are a popular choice for joining metals due to their strength, durability, and versatility. However, to achieve the best results, it is important to understand the science behind the chemical reaction that occurs during the bonding process.
This article will provide an in-depth look at the chemical composition of epoxy adhesives, the role of catalysts, surface preparation, the chemical reaction mechanism, factors affecting bond strength, temperature and moisture considerations, and a comparison to other metal bonding methods. Additionally, we will explore various industries that use epoxy adhesives for metal bonding and specific applications within each industry.
Chemical Composition of Epoxy Adhesives
Epoxy adhesives are a two-part system consisting of a resin and a hardener. The resin is typically a bisphenol A (BPA) or bisphenol F (BPF) based polymer that is liquid at room temperature. The hardener is usually an amine or polyamide that is also liquid at room temperature. When these two components are mixed together in the correct ratio, they undergo a chemical reaction known as curing. This reaction results in a solid material with excellent adhesive properties.
The role of each component in the bonding process is crucial. The resin provides the adhesive properties and determines the final properties of the cured material such as strength, flexibility, and chemical resistance. The hardener acts as a curing agent by reacting with the resin to form cross-links between polymer chains. This cross-linking process creates a three-dimensional network that gives the cured material its strength and durability.
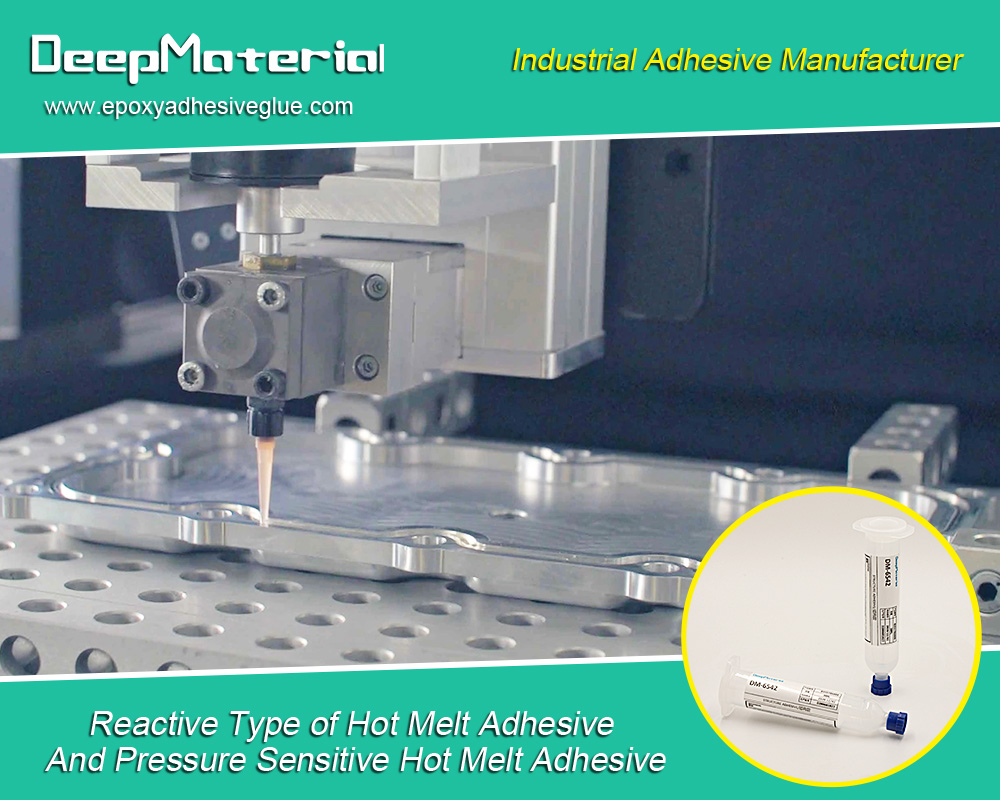
The Role of Catalysts in Epoxy Adhesive Bonding
Catalysts are substances that increase the rate of a chemical reaction without being consumed in the process. In epoxy adhesives, catalysts are used to speed up the curing process and improve bond strength. There are several types of catalysts used in epoxy adhesives including amine-based catalysts, anhydride-based catalysts, and Lewis acid catalysts.
Amine-based catalysts are the most commonly used type of catalyst in epoxy adhesives. They work by reacting with the hardener to form an intermediate compound that then reacts with the resin to form cross-links. Anhydride-based catalysts work by reacting with moisture in the air to form an acid that then reacts with the hardener to initiate curing. Lewis acid catalysts work by coordinating with the hardener to activate it for curing.
The Importance of Surface Preparation in Metal Bonding
Surface preparation is crucial for achieving a strong bond between metals using epoxy adhesives. The surface must be clean, dry, and free from any contaminants such as oil, grease, or rust. Any surface irregularities such as scratches or pits must also be removed to ensure maximum contact between the adhesive and metal surfaces.
The steps involved in surface preparation include cleaning the surface with a solvent such as acetone or alcohol, sanding or grinding to remove any surface irregularities, and then cleaning again with a solvent to remove any remaining contaminants.
The Chemical Reaction Mechanism of Epoxy Adhesives
The chemical reaction mechanism of epoxy adhesives involves three main steps: mixing, induction period, and curing. During mixing, the resin and hardener are combined in the correct ratio and mixed thoroughly to ensure even distribution of both components.
During the induction period, there is no visible change in the mixture as it begins to react slowly. This period can last from several minutes to several hours depending on factors such as temperature and humidity.
During curing, cross-linking occurs between polymer chains resulting in a solid material with excellent adhesive properties. The curing process can take anywhere from several hours to several days depending on factors such as temperature and humidity.
Factors Affecting the Strength of Epoxy Adhesive Bonds
Several factors can affect the strength of epoxy adhesive bonds including temperature, humidity, and pressure. Temperature affects bond strength by influencing the rate of curing. Higher temperatures generally result in faster curing times but can also lead to reduced bond strength if temperatures exceed optimal ranges.
Humidity affects bond strength by interfering with curing reactions that rely on moisture such as anhydride-based catalysts. High humidity can slow down curing times or prevent curing altogether if moisture levels are too high.
Pressure affects bond strength by ensuring maximum contact between metal surfaces during curing. Applying pressure during curing can help eliminate any air pockets or gaps between metal surfaces resulting in a stronger bond.
The Role of Temperature in Epoxy Adhesive Bonding
Temperature plays a critical role in epoxy adhesive bonding as it affects both curing time and bond strength. Optimal temperature ranges for bonding vary depending on specific adhesive formulations but generally fall between 60°F-80°F (15°C-27°C). Temperatures outside this range can lead to reduced bond strength or longer curing times.
The Effect of Moisture on Epoxy Adhesive Bonding
Moisture can have both positive and negative effects on epoxy adhesive bonding depending on specific adhesive formulations and curing mechanisms. Anhydride-based catalysts rely on moisture for activation but high humidity levels can interfere with other types of catalysts leading to reduced bond strength or longer curing times.
To prevent moisture from interfering with bonding processes it is important to store adhesives properly in sealed containers away from sources of moisture such as water or high humidity environments.
Comparing Epoxy Adhesives to Other Metal Bonding Methods
Epoxy adhesives offer several advantages over other metal bonding methods such as welding or soldering including lower heat input requirements, greater design flexibility, and improved fatigue resistance. However, they may not be suitable for all applications depending on specific requirements such as load-bearing capacity or environmental exposure.
Applications of Metal Bonding Epoxy Adhesives in Various Industries
Epoxy adhesives are widely used across various industries for metal bonding applications due to their versatility and effectiveness. In automotive applications they are used for body panel bonding and structural repairs while aerospace applications include composite bonding and repair work.
In construction applications they are used for concrete anchoring and structural steel bonding while marine applications include hull repairs and composite bonding.
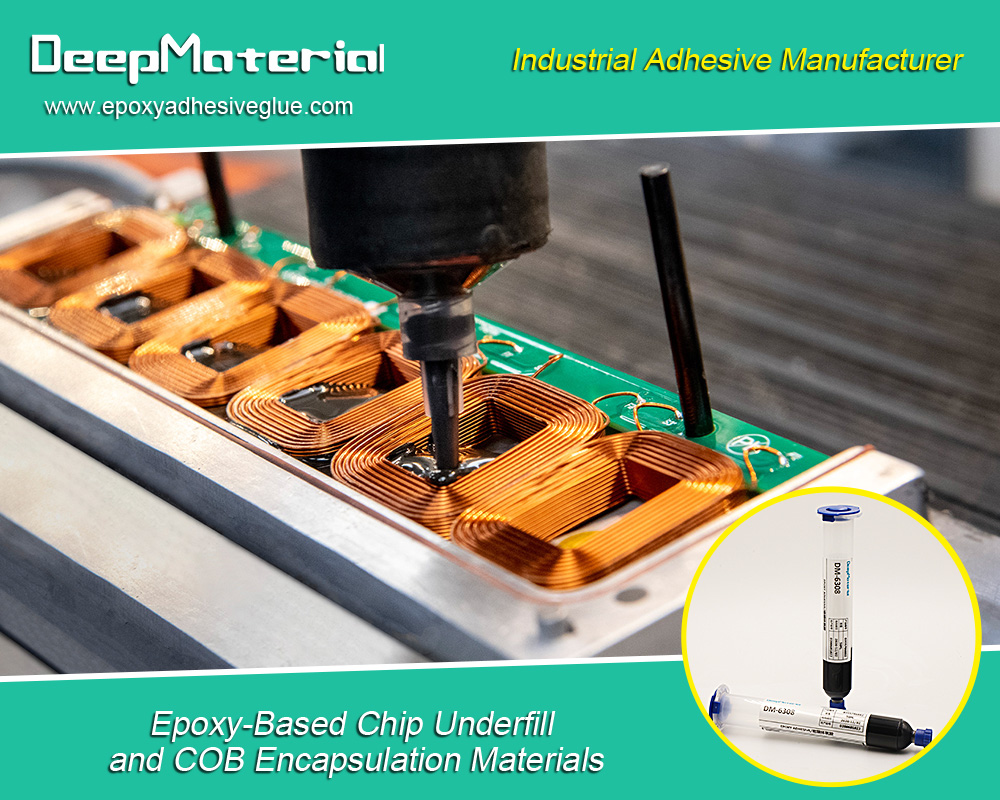
Conclusion
Understanding the science behind metal bonding epoxy adhesives is crucial for achieving strong bonds between metals across various industries including automotive, aerospace, construction, marine, and more. Factors such as temperature, humidity, pressure, surface preparation, and catalyst selection all play critical roles in achieving optimal results when using epoxy adhesives for metal bonding applications.
For more about choosing the Metal Bonding Epoxy Adhesives, you can pay a visit to DeepMaterial at https://www.epoxyadhesiveglue.com/epoxy-adhesive-for-metal/ for more info.