Can Electronic Potting Material Be Used For High-Frequency Applications?
Can Electronic Potting Material Be Used For High-Frequency Applications?
Electronic potting material serves as an essential protective shield for electronic components and devices from any environmental factors like moisture, dust, or even vibrations. It also contributes immensely to the reliability and long-term sustainability of these electronic gizmos in high-frequency applications such as telecommunications, wireless communication systems, radar systems, and lightning-speed data transmission.
Such shielding ensures the delicate parts are kept safe from any sharp impulses or damage caused otherwise; using this friend in need ensures a solid backup plus much peace of mind.
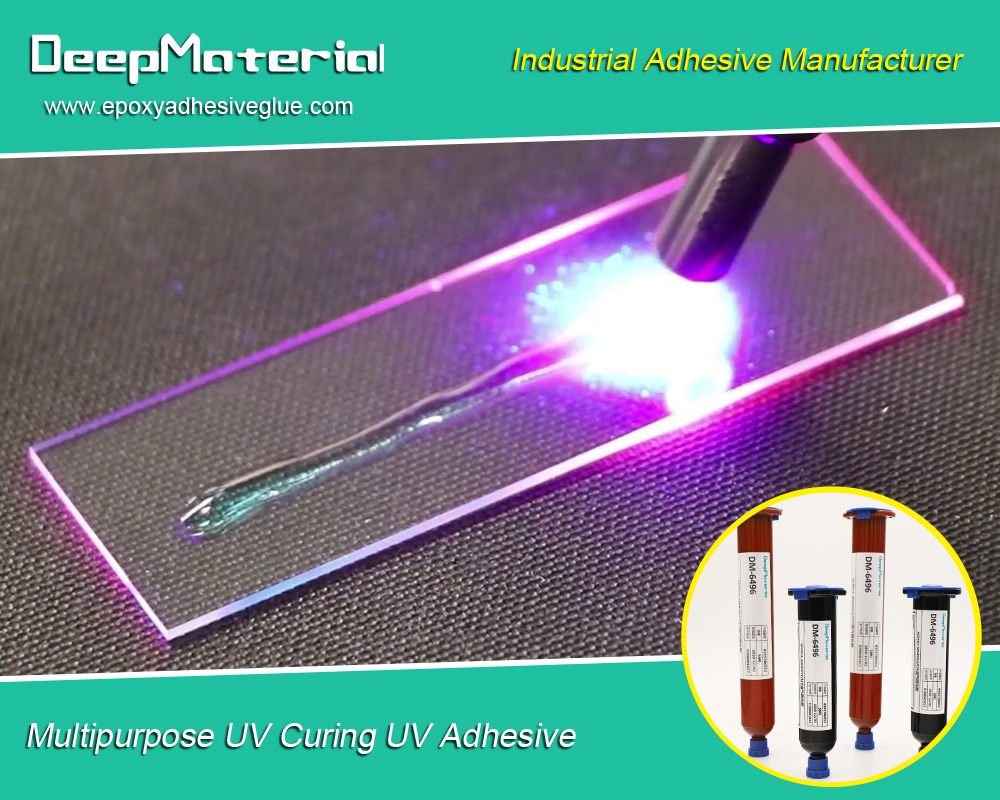
What Are High-Frequency Applications?
High-frequency applications are an absolute must for modern electronics. We’re talking about signals that shoot up beyond 1GHz, and they make it possible to transfer tremendous amounts of data extremely quickly. Think Wi-Fi, cellular networks, and Bluetooth — all of them highly depend on these ultra-fast frequencies. They’ve also opened the door to things like aviation and military radars and the speedy data transmissions used in telecommunications and data centers.
These high-frequency applications have completely revolutionized different industries—no exaggeration! Wireless connectivity became common knowledge practically overnight, the same with real-time data processing and fast internet access, which we now can’t seem to live without. These apps have changed today’s world.
Challenges in Using Electronic Potting Material for High-Frequency Applications
Utilizing electronic potting material in high-frequency components presents many unique problems. Most significantly, signal issues frequently arise from the lack of integrity these signals maintain while passing through this medium – leading to diminished performance and output.
Additionally, any electronic device which operates at such high frequencies necessitates excellent thermal conductivity amongst its potting material; otherwise, heat will not dissipate effectively.
Electrical properties, thermal properties, chemical properties, and mechanical qualities all affect how this material functions in specific settings, highlighting the complexity of applications when using epoxy or other materials for this purpose.
Factors to Consider When Selecting Electronic Potting Material for High-Frequency Applications
When it comes to potentially high-stakes situations, such as selecting electronic potting material for your hi-tech applications, key elements can’t be overlooked.
First and foremost, think about the electrical properties; what’s the dielectric constant? Does it have a low-dissipation factor?
Secondly, assess the heat – is its thermal conductivity suitable? Is the coefficient of thermal expansion compatible with that of other materials in contact with it?
The chemical course is next – will this harmonize without clashes between its constituents?
Finally, take a peek into how rugged the potting material should be. Will its hardness protect against mechanical shock and vibration while still being flexible enough when circumstances demand it?
With these careful considerations of all aspects mentioned above strung together like beads on an abacus, you won’t miss a beat and ensure violins remain unharmed.
Types of Electronic Potting Material Suitable for High-Frequency Applications
Selection of the right potting material for high-frequency applications can be overwhelming.
Epoxy-based is one commonly used option owing to its outstanding electrical insulation qualities and unbeatable strength; however, silicone-based scores point to flexibility and resistance to moisture or chemicals.
Polyurethane has excellent insulating properties and reliability, and acrylic fetches admiration for firming up quickly with a superior adherence power.
Choose wisely, considering all characteristics that your project demands – what could ultimately make the difference between success or failure?
Advantages of Using Electronic Potting Material for High-Frequency Applications
With electronic potting material, high-frequency applications provide a ton of perks. For starters, it acts like armour against the naughty things Mother Nature throws our way – like moisture, dust and nasty vibrations, which can damage your electronics.
Plus, your components are in for a snug hug – this helps keep them stable while providing unbeatable electrical insulation so you don’t have to worry about breakdowns or short circuits.
And if that weren’t enough already, it also ups the thermal conductivity factor big time, meaning heat is kept at bay and stays away from your sensitive gadgets!
Limitations of Using Electronic Potting Material for High-Frequency Applications
Electronic potting material is a popular go-to for shielding delicate electronic components from potentially harmful elements, such as moisture, dust and vibration.
But before you use the stuff in high-frequency operations, consider its limitations, which include distortions and attenuations brought about by frequencies passing through it.
It could be better if transmitting over telecommunications equals mission-central! In addition, removing this stabilizing layer can be hassle-central when making repairs or modifications – likely costing both time and money – making all involved very grumpy.
Then, there’s the chance that interference may occur, resulting in signal distortion because of how it interacts with the components, which you do not want if those bits are susceptible.
Testing Methods for Electronic Potting Material in High-Frequency Applications
Several testing methods are available to determine if a potting material is suitable for high-frequency applications. A constant dielectric measurement checks how well it transmits signals without losing or distorting them.
Dissipation factor measurement indicates how much energy is lost in the potting material when subjected to high frequencies; Thermal conductivity determines its heat dispersion capabilities, while tensile strength assessment proves its mechanical stability and durability.
All these measurements provide an accurate picture of whether or not said potting material can live up to expectations.
Future Developments in Electronic Potting Material for High-Frequency Applications
The future of electronic potting material for high-frequency applications is a real success story! Material science is advancing in leaps and bounds, paving the way to develop improved versions of potting materials with amplified electrical, thermal, chemical and mechanical properties.
Plus, new testing techniques are being designed to precisely scrutinize how well these work when used in high-frequency applications. Additionally, integrating potting material with other cutting-edge technologies – such as nanotechnology and additive manufacturing – will increase their ability and performance.

Last words
The electronic potting material is necessary for high-frequency applications, adding stability and protection to electronic components. Challenges and limitations exist with this material, but science and testing methods are always making it better tailored to the needs of the job. With careful selection and assessment, these materials can be counted on to perform reliably in higher frequency scenarios – no matter how tough they get.
For more about choosing the best Electronic Potting Material, you can pay a visit to DeepMaterial at https://www.epoxyadhesiveglue.com/category/epoxy-adhesives-glue/ for more info.