Best Adhesive For Bonding Metal To Metal Techniques You Must Know
Best Adhesive For Bonding Metal To Metal Techniques You Must Know
In manufacturing, construction, and DIY projects, the need to bond metal to metal is a common occurrence. The process may seem straightforward, but it’s not as simple as slapping on some glue and hoping for the best. The type of adhesive you use, the surface preparation, and the application technique can all significantly impact the strength and durability of the bond.
In this guide, we will delve into the best adhesive for bonding metal to metal techniques that you must know. Whether you’re a seasoned professional or a novice DIY enthusiast, this blog post will equip you with the knowledge and skills to create strong, lasting bonds between metal surfaces.
Advantages and Disadvantages of Different Bonding Techniques
There are several different techniques available for metal bonding, each with its own advantages and disadvantages. The choice of bonding technique depends on factors such as the type of metals being bonded, the desired strength of the bond, and the specific requirements of the application.
One common bonding technique is adhesive bonding, which involves the use of adhesives to join metal components together. Adhesive bonding offers several advantages, including the ability to bond dissimilar metals, excellent load distribution, and the ability to create complex shapes. However, adhesive bonding may not be suitable for high-temperature applications or applications where the bond needs to be disassembled.
Another common bonding technique is welding, which involves melting the metal surfaces to be joined together and allowing them to solidify. Welding offers excellent strength and durability, making it suitable for applications where a strong bond is required. However, welding can be time-consuming and may require specialized equipment and skilled operators.
Soldering and brazing are two other bonding techniques that involve the use of a filler metal to join metal components together. Soldering is typically used for low-temperature applications, while brazing is used for high-temperature applications. Both techniques offer good strength and reliability, but they may not be suitable for applications where a very strong bond is required.
Surface Preparation for Metal Bonding
Surface preparation is a critical step in the metal bonding process, as it ensures that the metal surfaces are clean and free from contaminants, such as dirt, grease, and oxide layers. Proper surface preparation is essential for achieving a strong and durable bond between the metal components.
The first step in surface preparation is cleaning the metal surfaces using a suitable solvent or detergent. This removes any dirt, grease, or oil that may be present on the surfaces. After cleaning, the surfaces should be rinsed with clean water and dried thoroughly.
The next step in surface preparation is removing any oxide layers that may be present on the metal surfaces. This can be done using mechanical methods, such as sanding or grinding, or chemical methods, such as acid pickling or chemical etching. The goal is to expose clean metal surfaces that are free from oxide layers.
After removing the oxide layers, the metal surfaces should be treated with a suitable primer or adhesion promoter. This helps to improve the adhesion between the metal surfaces and the adhesive or filler metal. The primer or adhesion promoter should be applied according to the manufacturer’s instructions and allowed to dry before proceeding with the bonding process.
Welding Techniques for Metal Bonding
Welding is a widely used technique for metal bonding, as it offers excellent strength and durability. There are several different welding techniques available, each with its own advantages and disadvantages.
One common welding technique is arc welding, which involves the use of an electric arc to melt the metal surfaces to be joined together. This can be done using different types of welding machines, such as TIG (tungsten inert gas) welding, MIG (metal inert gas) welding, or stick welding. Arc welding offers excellent strength and durability, making it suitable for applications where a strong bond is required. However, it can be time-consuming and may require skilled operators.
Another common welding technique is resistance welding, which involves the use of electrical resistance to generate heat and melt the metal surfaces to be joined together. This can be done using different types of resistance welding machines, such as spot welding or seam welding. Resistance welding offers fast and efficient bonding, making it suitable for high-volume production. However, it may not be suitable for all types of metals or applications.
Laser welding is another welding technique that uses a high-energy laser beam to melt the metal surfaces to be joined together. Laser welding offers precise control and high welding speeds, making it suitable for applications where accuracy and speed are important. However, it may require specialized equipment and skilled operators.
Soldering and Brazing Techniques for Metal Bonding
Soldering and brazing are two techniques that involve the use of a filler metal to join metal components together. These techniques offer good strength and reliability, making them suitable for a wide range of applications.
Soldering is typically used for low-temperature applications, where the melting point of the filler metal is below 450°C (840°F). It involves heating the metal surfaces to be joined together and applying the solder to create a bond. Soldering offers good electrical conductivity and is commonly used in electronics and plumbing applications. However, it may not be suitable for high-temperature applications or applications where a very strong bond is required.
Brazing, on the other hand, is used for high-temperature applications, where the melting point of the filler metal is above 450°C (840°F). It involves heating the metal surfaces to be joined together and applying the brazing alloy to create a bond. Brazing offers excellent strength and durability and is commonly used in the automotive, aerospace, and HVAC industries. However, it may require specialized equipment and skilled operators.
Mechanical Fastening Techniques for Metal Bonding
Mechanical fastening is another technique that can be used for metal bonding. This involves the use of mechanical devices, such as screws, bolts, nuts, or rivets, to join metal components together. Mechanical fastening offers several advantages, including ease of assembly and disassembly, high strength, and reliability. It is commonly used in applications where a strong and durable bond is required, such as construction, automotive, and aerospace.
There are several different mechanical fastening techniques available, each with its own advantages and disadvantages. Some common mechanical fastening methods for metal bonding include screw fastening, bolt fastening, nut fastening, and riveting.
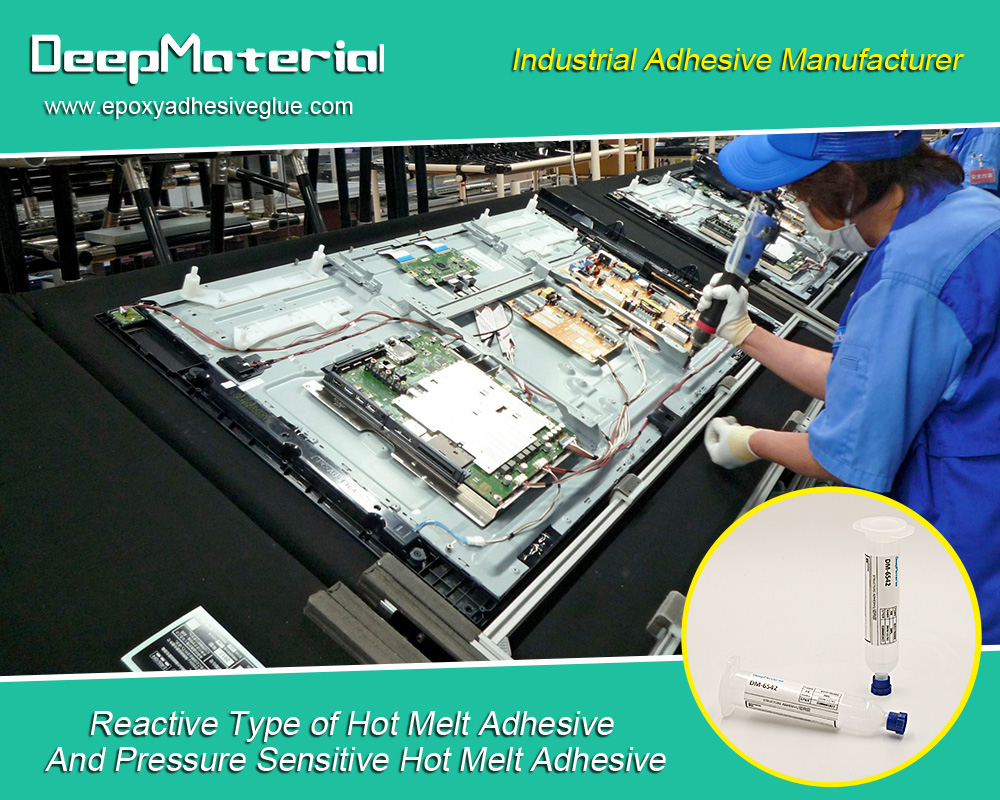
Wrapping It Up
Metal bonding is an essential process in many industries, allowing for the creation of strong and durable connections between metal components. There are several different bonding techniques available, each with its own advantages and disadvantages. The choice of bonding technique depends on factors such as the type of metals being bonded, the desired strength of the bond, and the specific requirements of the application.
For more about choosing the Best Adhesive For Bonding Metal To Metal Techniques You Must Know, you can pay a visit to DeepMaterial at https://www.epoxyadhesiveglue.com/category/epoxy-adhesives-glue/ for more info.