Achieving Optimal Strength with UV Cure Adhesive for Glass: A How-To Guide
Achieving Optimal Strength with UV Cure Adhesive for Glass: A How-To Guide
In today’s era of advanced manufacturing and complex do-it-yourself projects, finding an adhesive that delivers strength, clarity, and quick curing times can be a challenge. However, UV cure adhesive for glass emerges as a standout solution for both enthusiasts and professionals seeking high-performance bonding.
This cutting-edge adhesive technology utilizes ultraviolet light to secure bonds that are not only strong but also precise and durable, making it a go-to choice for projects that demand exactness and longevity.
This guide aims to walk you through the steps to maximize the strength of UV cure adhesive for glass bonding. Covering everything from surface preparation, adhesive application, to the curing process, we’ll equip you with the necessary insights to achieve a perfect, enduring bond.
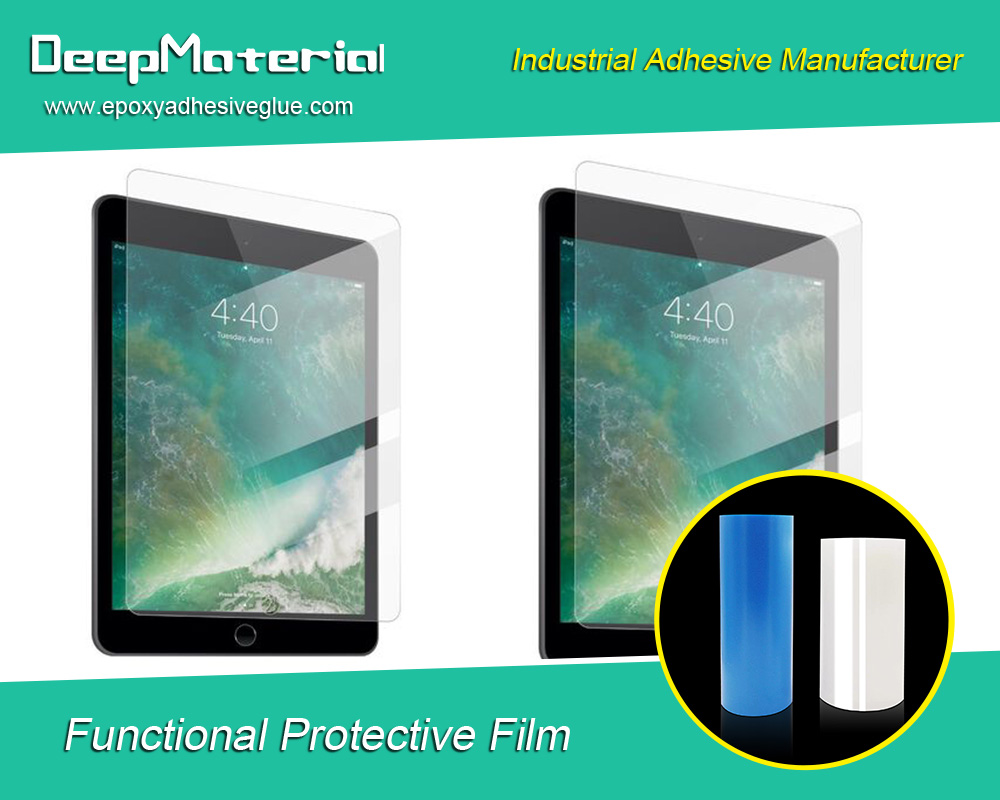
Advantages of Using UV Cure Adhesive for Glass
UV cure adhesive for glass stands out for its quick curing time, offering a significant advantage over traditional adhesives which may take hours or days to fully set. This rapid curing capability, activated by UV light exposure, accelerates assembly and production, enhancing efficiency.
Additionally, the adhesive forms a stronger bond due to a chemical reaction that creates a durable cross-linked polymer network, ideal for industries needing robust and lasting adhesion like automotive, aerospace, and electronics.
Moreover, UV cure adhesive outperforms other adhesives in temperature and moisture resistance, maintaining its properties under extreme conditions and in humid environments, thus ensuring the durability of bonded components. Another benefit is its elimination of the need for clamping or pressure during curing, simplifying the bonding process, saving time, and reducing costs, making it an efficient and cost-effective choice for glass bonding projects.
Factors that Affect the Strength of UV Cure Adhesive for Glass
To achieve optimal bond strength when using UV cure adhesive for glass, several factors need to be taken into consideration. These include surface preparation, type of glass, quantity of adhesive applied, and curing time and intensity.
Surface Preparation
The glass surface must be thoroughly cleaned to remove any dirt, dust, oils, or contaminants that could interfere with the bonding process. This can be done using a suitable solvent or cleaner specifically designed for glass surfaces. After cleaning, it is important to ensure that such surface is completely dry before applying the adhesive.
The Type of Glass
Different types of glass have different surface properties and compositions, which can impact the adhesion of the UV cure adhesive. It is essential to choose an adhesive that is compatible with the specific type of glass being bonded to ensure optimal bond strength. Consulting with the adhesive manufacturer or supplier can help in selecting the right adhesive for the specific glass type.
The Quantity of Adhesive Applied
Applying too little adhesive may result in a weak bond, while applying adhesive in too much quantity will likely cause excess squeeze-out as well as potential bonding issues. It is important to follow the manufacturer’s recommendations regarding the proper amount of adhesive to be applied for each specific application. This ensures that the adhesive is evenly distributed and provides sufficient coverage for a strong bond.
Curing Time And Intensity
The adhesive must be exposed to the appropriate intensity of UV light for the recommended curing time to ensure complete curing and maximum bond strength. Insufficient curing time or inadequate UV light intensity can lead to a bond that is weak. This may fail under stress or load. It is important to follow the manufacturer’s instructions regarding the recommended curing time and intensity for the specific adhesive being used.
Preparing the Glass Surface for UV Cure Adhesive Application
Cleaning The Glass Surface
Use a glass-specific solvent or cleaner with a lint-free cloth to eliminate dirt, dust, oils, or any contaminants, ensuring a clean surface for adhesive application.
Removing Any Contaminants
After cleaning, inspect and remove any remaining dirt or debris with a clean cloth or brush, focusing on corners and edges to fully clear such surface.
Drying The Surface
Ensure the glass is completely dry by using a clean cloth or natural air drying. Avoid compressed air or heat to prevent contamination or glass stress.
By meticulously preparing the glass surface through these steps, you can enhance the adhesion and durability of the UV cure adhesive bond, contributing to the success of your project.
Applying UV Cure Adhesive to Glass: Step-by-Step Guide
Choosing The Right Applicator
Pick an appropriate applicator like syringes, brushes, or automated systems for the adhesive. Ensure it’s clean and contaminant-free.
Applying The Adhesive Evenly
Apply a thin, uniform layer of UV cure adhesive on the glass using gentle, consistent pressure to avoid excessive adhesive and bonding issues.
Avoiding Air Bubbles
Apply the adhesive slowly in a zigzag or spiral pattern to prevent air bubbles, ensuring a smooth and even layer.
Removing Excess Adhesive
After application, remove any excess adhesive with a clean, lint-free cloth or tool, being careful not to disturb the applied adhesive for an even bond.
Adhering to these steps ensures correct and uniform application of UV cure adhesive on glass, enhancing adhesion, bond strength, and the longevity of the glass components.
Curing UV Cure Adhesive for Glass: Best Practices
Choosing The Right UV Light Source
Pick a UV light source compatible with your adhesive, as different adhesives require specific wavelengths or intensities for effective curing. Consult the adhesive’s manufacturer or supplier for guidance on the best UV light source for your application.
Positioning The Light Source Correctly
Place the UV light at the recommended distance and angle, as per the adhesive manufacturer’s instructions, to ensure even curing. Make sure the entire adhesive area receives UV light exposure for uniform curing.
Ensuring Proper Curing Time And Intensity
Adhere to the manufacturer’s guidelines for the curing time and intensity specific to your adhesive. Avoiding over-curing or under-curing is crucial to prevent incomplete curing or weak bond.
Adhering to these best practices ensures proper curing of UV cure adhesive, leading to a strong, durable bond on the glass surface. Correct curing is key to achieving the best bond strength and the reliability of the bonded glass components.
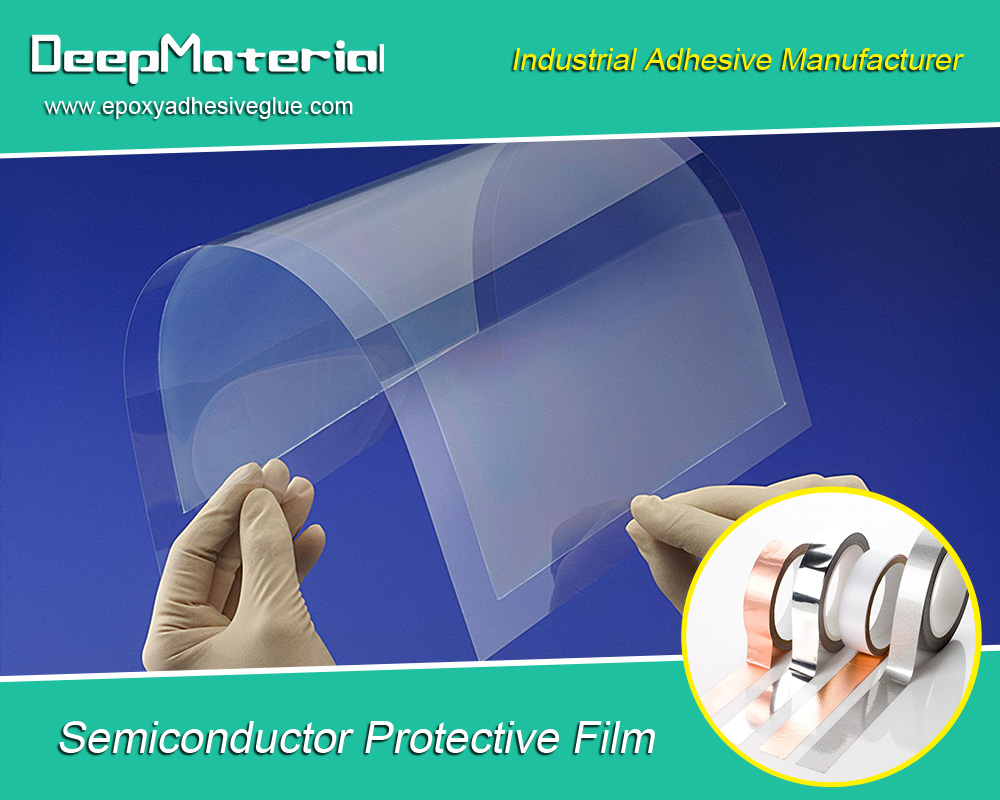
Conclusion
To ensure optimal curing of UV cure adhesive, select a UV light source that aligns with the adhesive’s specific requirements, consulting the manufacturer for guidance. Correctly position the UV light as recommended to guarantee even exposure across the entire adhesive area. Follow the manufacturer’s instructions on curing time and intensity closely to avoid weak bonds due to over or under-curing. Proper curing practices result in a strong, durable bond and reliable glass components.
For more about choosing the best UV cure adhesive for glass, you can pay a visit to DeepMaterial at https://www.epoxyadhesiveglue.com/category/epoxy-adhesives-glue/ for more info.